Introduction
An emerging trend over the last two to three years has been to add layers of thermal insulation and flame/gas impingement barriers between the pouch and prismatic format cells in a battery pack to prevent thermal propagation. This passive thermal management solution has been shown to effectively prevent propagation without adding excessive weight to the battery.
The obvious downside of this method is that the battery cells are surrounded by insulation, and there is no easy path for the internal heat of the cells to spread to the environment outside of the pack. There is only one point of thermal contact between the cells, the thermal interface, and the cold plate. This is at the bottom surface of the cell, where there is very little contact area and often an inferior thermal path from the hot components of the interior of the cell to the cold plate.
How do you fix the problems caused by using an insulation-only strategy? It’s simple: Add NeoGraf Solutions’ SpreaderShield™ thin, flexible, and lightweight graphite heat spreader to the battery pack.
Thermal Propagation Prevention Methods
There are currently four primary methods to prevent thermal propagation in battery prismatic and pouch cell packs. These propagation prevention methods all have significant consequences for cell cycle lifetime, the ability to fast charge, and an increase in driving range. These methods are used individually or combined, with each manufacturer adding their experience to produce the best results.
Isolation
In the isolation method, the modules are placed within a heat-resistant battery pack housing. If there is a cell failure, there will be sufficient time for the electric vehicle (EV) to stop and allow passengers to safely exit the vehicle. The most common escape time requirement is five minutes.
Isolation is often considered the least expensive way to meet the five-minute escape time requirement. These packs have high energy density and high specific energy. Construction is simple and cost-effective.
Since the failure of an individual cell may generate a hot spot on the battery pack housing, various thermal insulations and heat-spreading materials are used inside the housing to protect its integrity. These materials can include SpreaderShield™ flexible graphite, mica, aerogel, air gaps, metals, and ceramics. Even if there is a cascading failure, the heat will be widely distributed on the housing surface, helping it maintain its physical integrity throughout the failure event.
An alternate strategy is to place a fire-retardant coating on the outside of the battery pack housing. Intumescent materials, such as NeoGraf’s GrafGuard™ expandable graphite flakes mixed in with a resin binder, can make for a very robust flame barrier layer.
When isolation is the primary propagation prevention method, the individual cells often have inadequate thermal management. Cell temperature and cell temperature gradients generally are not tightly controlled. Fast charging and discharging can overheat and damage the cells, limiting cell cycle lifetimes. Thermal degradation of a single cell can significantly reduce the range of the overall battery pack.
Immersion
In the immersion method, the individual cells are partially or completely surrounded by a dielectric liquid, which is circulated throughout the module by a mechanical pumping and cooling system. This strategy is often seen as the ultimate method of preventing propagation. If a cell fails, the liquid will carry away the heat and stop the fire from spreading to the adjacent cells.
The cell temperatures and temperature gradients can be tightly controlled using the cooling liquid. The ability to fast charge and cell cycle lifetimes are typically excellent. In immersion, the system’s overall size, weight, and complexity must be considered. There may be pumps, chillers, valves, baffles, and piping that are not part of other systems. Although the pack’s baseplate size may be significantly reduced, the system may have a higher overall weight due to the needed volume of cooling liquid.
To date, this method has not been widely used in EVs. The cooling liquid itself may be considered a hazardous substance. Special maintenance, handling, and disposal rules may apply. Due to the system’s increased complexity, initial costs and maintenance may be higher than with other types of systems.
Insulation
In the popular insulation method, thermal insulation and flame/particle impingement materials are placed between battery cells. In a single-cell failure event, the heat will not spread to the adjacent cells before the failure event is over.
A combination of different materials, such as aerogel, fiberglass, phase-change, mica, polyimide, metals, and ceramics, are used to prevent heat from transferring to adjacent cells during a cell failure. Three to five millimeters of these materials are typically needed between cells to stop propagation.
Unfortunately, the insulation method of propagation control provides insufficient thermal management for the cells in all but the most favorable conditions. When the individual cells are enclosed in thermal insulating material, fast charging and rapid discharging will quickly raise the internal cell temperatures beyond the optimum of 25 – 35°C. Cells that run hot risk permanent internal damage.
Hot spots, primarily at the tabs, will not be effectively spread across the cells. Having large thermal gradients is another cause of premature cell aging. These abnormal thermal conditions will result in shorter cell cycle lifetimes and an increased risk of cell failure.
Fortunately, both of these problematic conditions are simple to overcome. By adding SpreaderShield thin, flexible graphite heat spreader, the overheating problems and large thermal gradients caused by an “insulation only” strategy are easily solved.
Spreading
To enable the insulation to be effective in day-to-day operations, a layer of SpreaderShield flexible graphite thermally spreading material needs to be added. The graphite is adhered directly against the cell, along the wide face, and extended down to the thermal interface. Depending on the level of thermal protection needed, the graphite is applied to one side of the cell or is looped around the bottom of the cell and adhered to both sides.
With the spreading method of thermal management, graphite performs two important functions. First, it spreads heat from the hot spots near the tabs over the entire face of the cell, reducing thermal gradients. Second, graphite provides a path for the cell’s heat to be spread down to the thermal interface and, ultimately, the cold plate.
The overall result of using graphite heat spreaders is that the cells can consistently maintain proper temperatures, even under harsh charging and operating conditions, giving extended cell cycle lifetimes. During a cell failure, the graphite works in conjunction with the insulation to prevent adjacent cells from failing.
Each of the four propagation methods is compiled into the chart below. The strengths and weaknesses of each method are highlighted.
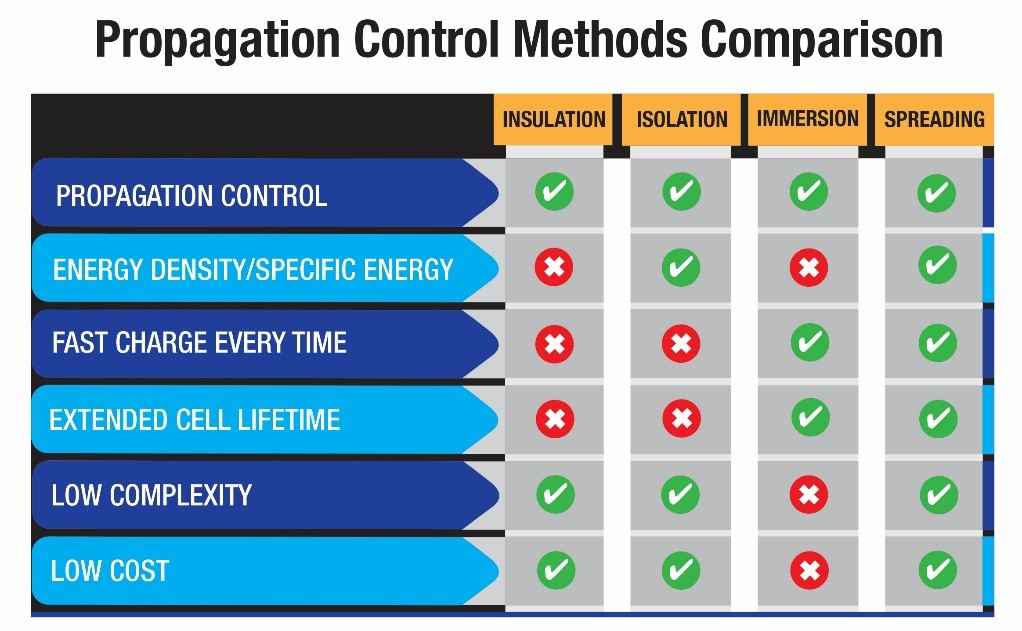
Conclusion
There are four primary ways to prevent thermal propagation in pouch and prismatic cell battery packs. These methods are isolation, immersion, insulation, and spreading. Of these, spreading not only prevents propagation but enables extended cell cycle lifetime, fast charging, and produces a battery pack that is small and lightweight. SpreaderShield flexible graphite heat spreaders are often used as the thermal management material in high-performance battery packs where a small and lightweight form factor is desirable.
# # # #
Author: Bret Trimmer – NeoGraf Solutions Applications Engineering Manager